Software Plan: Starter, Growth & Enterprise
Account Type: Seller Account, Aggregator & 3PL
Inventory Type: Serialized & Non-Serialized
Feature Description
The packing station is where the products are checked and packed before shipping. The station contains all kinds of materials that are required for packing. Packing stations are sometimes customizable according to the needs of the packer.
In this guide, we have explained the process that takes place in the packing station.
Go to -> Other settings
Check whether “Batch order processing mode” and “Activate Packing Station at B2C” for B2C are enabled. If not, please enable those.
If you wish to track the batch of the inventory that is being packed at the packing station, please enable the setting "Enable Batch Code Tracking at Packing Station"
Step 3: Create Batch
If the order is not created, use the (+) menu to create a new order.
If the order is already present, click on the “Create Batch” button.
Step 4: Add order to the batch.
Click on the (+) to add the order in the batch
Select the order and click on "Add to Batch"
The order will be added to the batch.
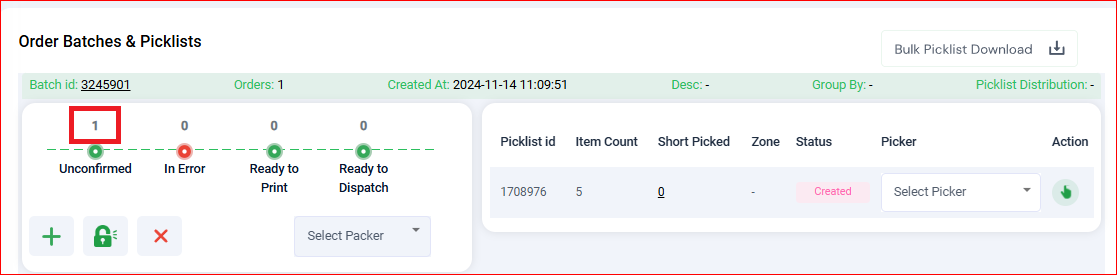
Step 5: Confirm the order
Click on the batch ID. The packer should select the orders to be processed further and click “Confirm” to confirm the order.
Step 6: Packing station
Click on “Packing station” from the “Print tab”. The order should be confirmed if it is unconfirmed.
Click on "Start Scanning"
If the SKU field is present, we need to scan it, and if the serial number field is present, we have to scan it. We also support Product EAN scan.
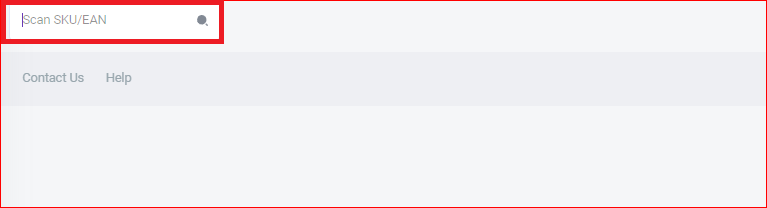
For B2C orders, the packer can select the batch from which he wishes to scan the items. Once the batch is selected, the packer will scan the item every time
To track the batches, please make sure that the config "Enable Batch Code Tracking at Packing Station" is enabled. If not, please go to Account Settings > Other Settings > Enable Batch Code Tracking at Packing Station.

The information on all items belonging to that batch will appear on this page.
Once all the items are scanned, the file is sent to the printer, and the invoice will be downloaded automatically.
Information about shipping labels and invoices will be printed
Finally, the order gets moved to the “Ready to Dispatch” tab.